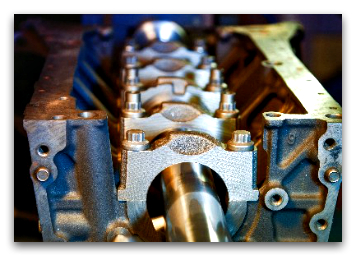
Ресурс дизелей определяется, в основном, износом кривошипно-шатунного механизма и цилиндро-поршневой группы. По этим причинам, например, дизели КамАЗ-740 согласно данным, направляются в капитальный ремонт в 78% случаев, из них на износ подшипников коленчатого вала приходится 43%, а на износ цилиндро-поршневой группы - 35%.
В нашем техническом центре комплексный ремонт ГБЦ включает перечень следующих операций:
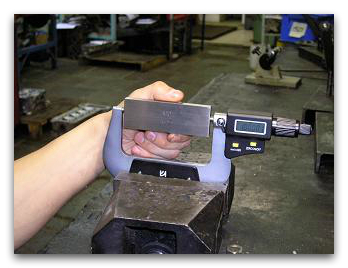
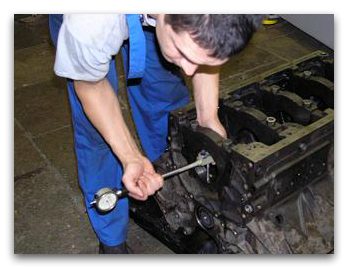
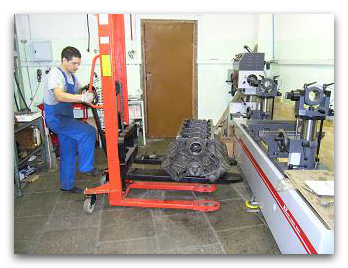
№
п/п |
Предельные отклонения
отверстий, мм |
Количество блоков | |
шт. | % | ||
1 | 0 ...+0,02 | 2 | 8 |
2 | +0,02 ...+ 0,04 | 8 | 32 |
3 | +0,04 ... +0,08 | 6 | 24 |
4 | +0,08 ... +0,12 | 2 | 8 |
5 | 0 ... - 0,02 | 3 | 12 |
6 | -0,02 ... –0,04 | 2 | 8 |
7 | -0,04 ... –0,08 и более | 2 | 8 |
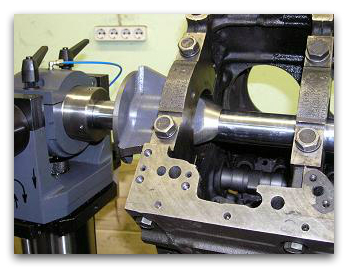
Межремонтный ресурс двигателей с невосстановленными параметрами коренных опор и посадочных поясков составляет 20…40% от ресурса нового двигателя. Если при этом несоосность коренных опор на длине 100 мм составляет 0,06 мм, то динамическая нагрузка на коленчатый вал увеличивается в 1,8 раза, а интенсивность изнашивания коренных вкладышей в 4 раза.
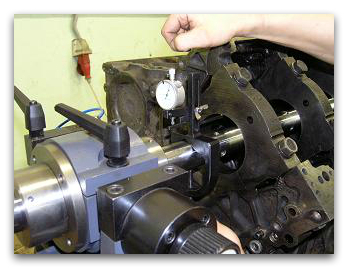
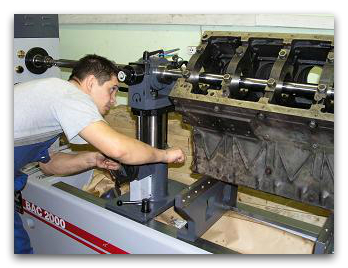
Примечание. Номинальный диаметр опор подшипников коленчатого вала дизеля КАМАЗ составляет 100,00+0,02мм.
Ремонтный диаметр опор подшипников коленчатого вала дизеля КАМАЗ составляет 100,50+0,02мм.
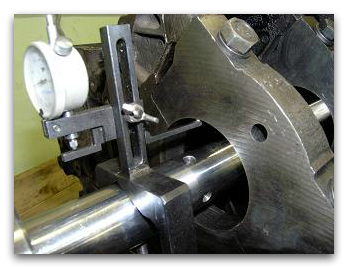
После установки бор-штанги в подвижные опоры производится предварительное центрирование бор-штанги относительно оси коленчатого вала с помощью специальных конусов (фото 4).
Более точное центрирование обеспечивается применением специальных контрольно-измерительных приспособлений фирмы AZ (фото 5, 6, 7).
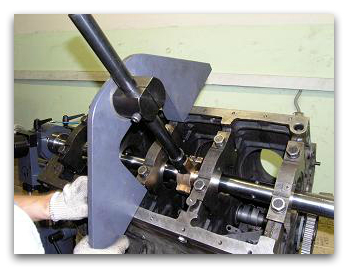
С целью повышения производительности труда и обеспечение необходимой жесткости инструментальной оснастки применяются специальные приспособления -«браслеты» (фото 9).
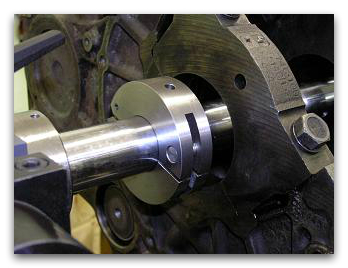
До обработки изношенные или восстановленные опоры подшипников имеют существенные отклонения от цилиндричности поэтому их обработку нужно производить в несколько этапов:
- черновая обработка (припуск от номинального или ремонтного размера должен составлять не более 0,1мм);
- получистовая обработка (припуск от номинального размера должен составлять ~ 0,03…0,04 мм) – фото 12;
- финишная обработка в размер.
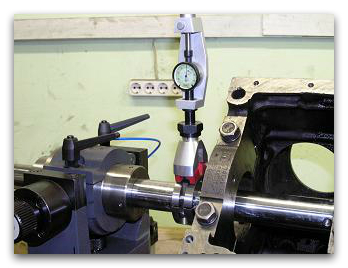
Для контроля размера опор на каждом этапе обработки фирма AZ рекомендует использовать специальный нутромер (фото 13), который позволяет производить измерения не снимая бор-штанги (фото 14).
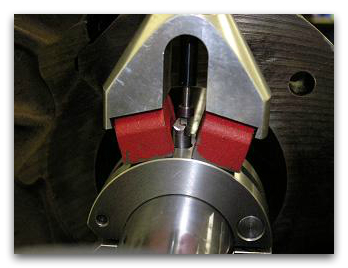
Выполнение этой операции позволяет существенно снизить шероховатость поверхности (фото 17) и, следовательно, улучшить качество сопряжения «опора –подшипник».
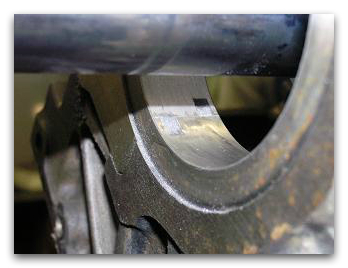
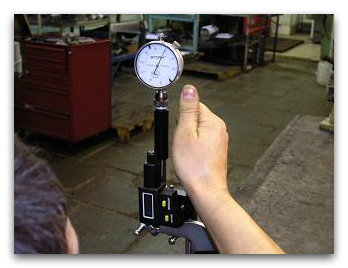
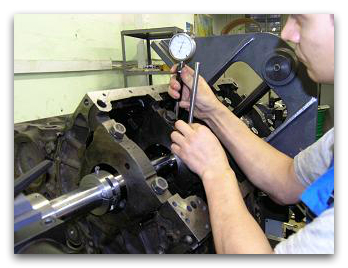
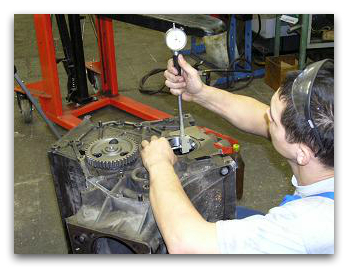
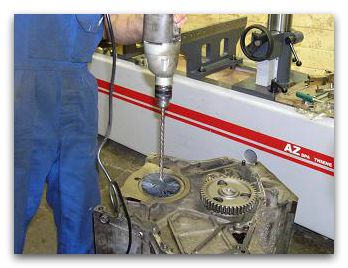
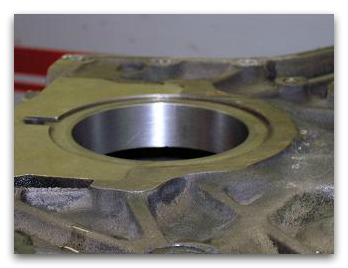